THANK YOU FOR SUBSCRIBING
Editor's Pick (1 - 4 of 8)
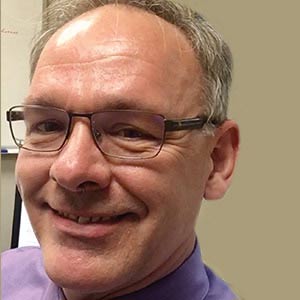
Steve Boebel, Vice President of Finance, Minuteman Internationa
By leveraging existing tools in SAP, we took a proactive approach and focused on the inventory items that were causing the biggest drain on capital.
Communication
Our legacy system was heavily dependent on spreadsheets and verbal communications. Frankly, it was manual nightmare. Morale was low and there was a lot of finger-pointing between departments. The Scheduling Planning Board is an interactive tool used to move and organize production. It provides a graphical presentation of the current factory planning schedule. Once the production planner updates the information, changes flow through SAP to the production floor. This process improvement was a huge improvement in both morale and productivity.
Demand Management
Demand management can be a struggle for any size company and we were no exception. Spreadsheets with every possible equipment configuration seemed to litter the executive conference room. For example, one scrubber model can have 176 different configurations. Any attempt to forecast every configuration would result in a forecast of more than 2,500 units when actual demand and capacity was 1,800. The extra 700 unit overage was the result of inflating the forecast for “just-in-case” scenarios. There was more inventory on the shelf then demand. To correct and enhance the forecast process, we utilized a method in SAP called Planning Bills of Material (BOMs). The 176 different BOM configurations were grouped by material similarities into six different planning BOM’s. The six planning BOM’s represented 80 percent of all the required material in all of the 176 different configurations. The remaining 20 percent of material was set up on individual forecasting or maximum/minimal stock levels. This movement generated not only lower inventory, but improved the overall forecasting process. Inventory levels where lowered due to fewer common parts being ordered and sitting on the shelf. At the completion of our project, we experienced an attitude adjustment towards SAP. Prior to the initiative, there was a strong grip on legacy solutions. Now, with a full understanding of SAP’s capabilities, the first question to a new problem is “What is SAP’s standard solution for this problem?”
Using Standard SAP Transaction Codes in the LIS (Logistics Information System) Module, We Zeroed In On Inventory Items That Would Yield the Largest Benefit